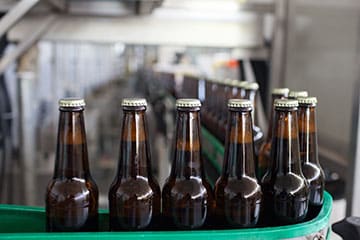
Brewery
Foam control technology delivering productivity gains, reduced beer losses, excellent oxygen/TPO values and elimination of CO2 bubble breakers.
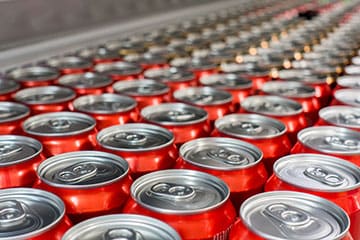
Beverage
Defoaming technology delivering filling speed gains, beverage loss & reject savings and increased filling temperature.
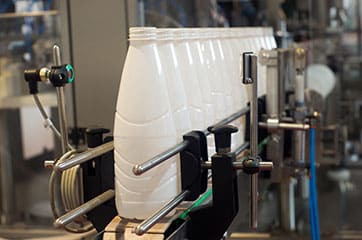
Dairy
Defoaming technology delivering hygiene & quality improvements, productivity and efficiency gains.
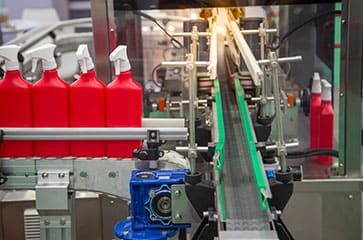
Chemical
Defoaming technology delivering elimination of contamination, quality improvements and productivity and efficiency gains.
Proven Results
Enjoyed by businesses around the globe
Increased Productivity
Filling speed increase, longer run times, reduced down time to cleaning
Deliver on Corporate KPIs
Reduced energy, waste, water consumption and CO2 consumption
Production Efficiency Gains
Reduced liquid losses, can & bottle rejects and waste
Energy Saving
Increased filling temperature, Reduced energy during chilling & pasteurization step
Waste Reduction
Reduced product liquid waste, water washers & chemicals during cleaning cycles
Hygiene & Quality Improvements
Eliminate contamination & microbiological risk on caps, seals, package
Delivering defoaming technology solutions with an ROI in under one year
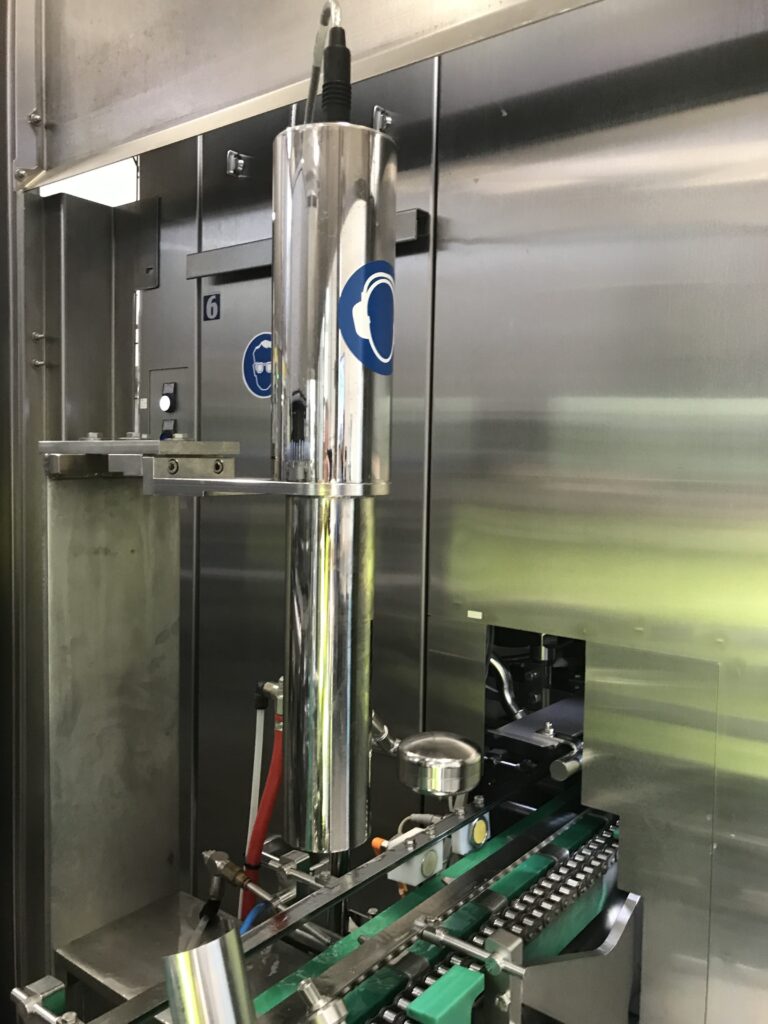
Defoaming Unit
Low energy cost, low operational cost, minimal down time for installation (less than 1 hour), fully automated to filler plc, stainless steel 316 material spec, IP67 water proof design, fully resistant to all chemicals during CIP cleaning process, polished steel surface for hygienic design.
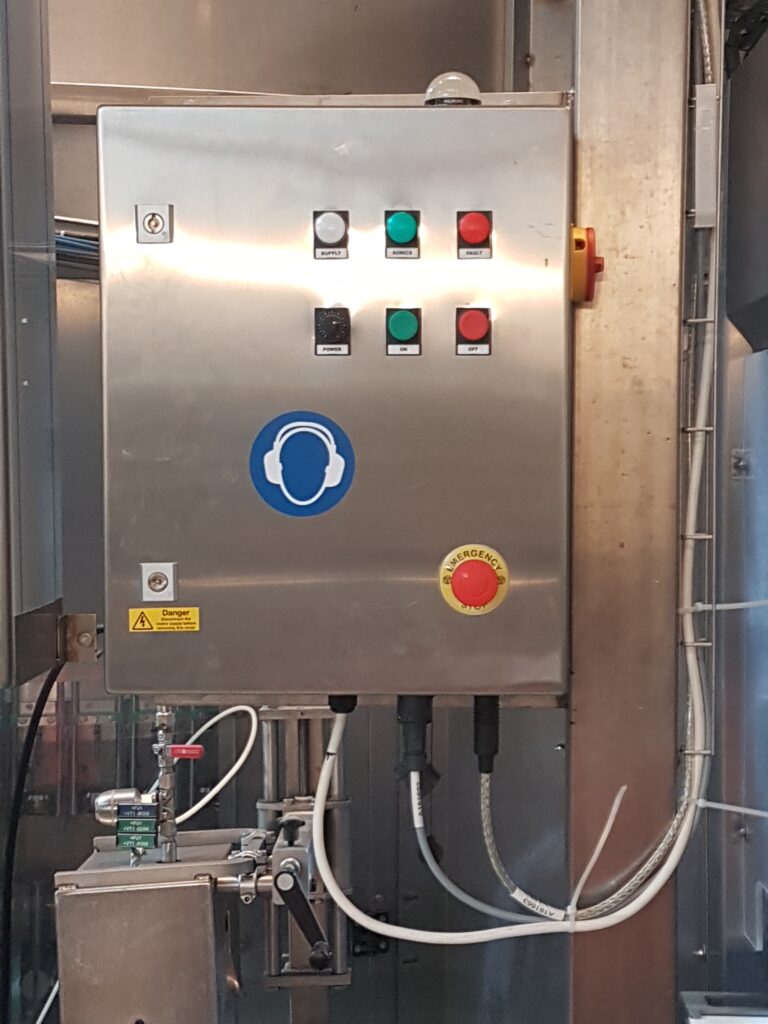
Cabinet
Mounting outside of the filler (wall mounting or stand), Power requirements: Single phase 110-240v, 12A, power/amplitude control & adjustability, cabinet control panel fully automated to filler plc, stainless steel design material spec, water proof design, fully resistant to all chemicals during cleaning process, light beacon for operation/standby and alarm fault, minimal down time for installation (less than 2 hour).